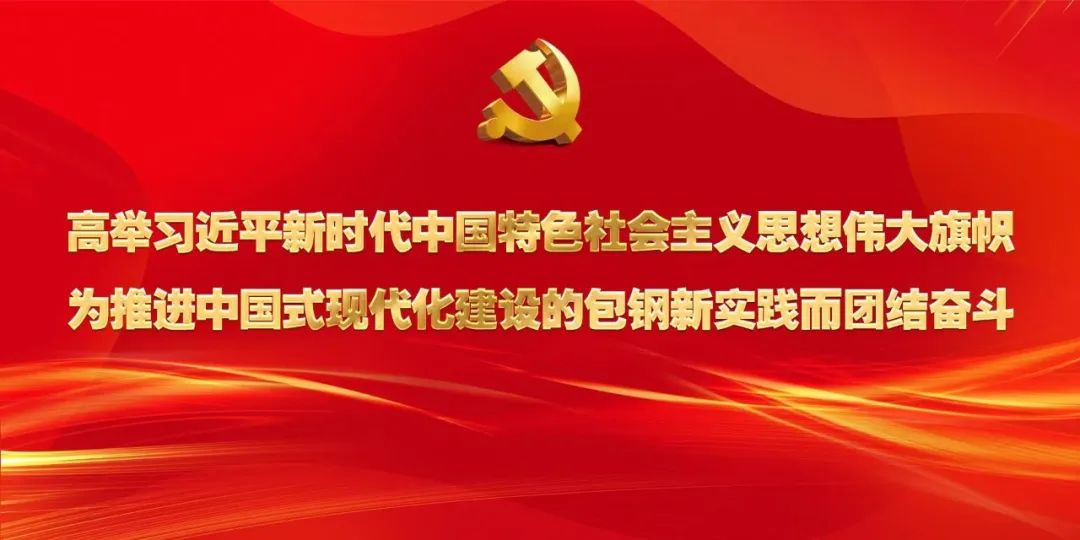
12月5日,包钢股份稀土钢板材厂1号450吨吊车点检机器人完成调试正式投入运行,标志着该厂自主实施的吊车智能化推进工程取得阶段性成果。这台集成走行控制、视觉识别、网络传输系统功能等设备的机器人,由稀土钢板材厂技术人员自行整合设计、施工、调试完成,是包钢股份首台吊车点检机器人,达到行业领先水平。
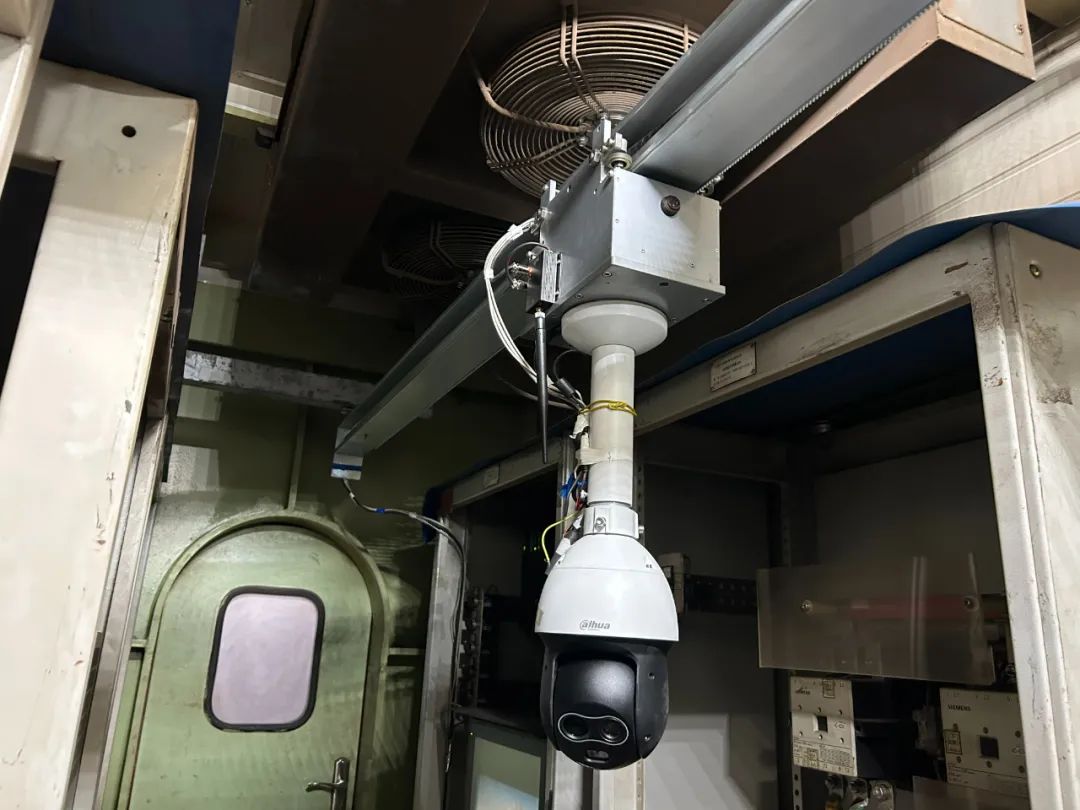
降钩,挂耳轴,提起铁水包,兑入铁水……稀土钢板材厂1号转炉前,1号450吨吊车流畅完成“兑铁”操作。“这是控制系统上千个电子原件协同控制的结果。”吊运作业部吊车电气区域技术主管贾伟一边翻看手机上的吊车远程集控页面一边说道。在吊车箱梁中,此时,一台悬挂在轨道上的机器人前后移动位置,转动黑色的“大眼睛”,观察着周边的电气设备,并且实时传送出设备信息。
接触不良引发的高温是吊车电气设备常见的故障之一,所以温度是吊车点检员最关注的参数之一。吊车集控室中,吊运作业部炼钢吊车点检员赵延斌坐在电脑前点击鼠标。“24小时无死角守护,机器人实在太能干了!”数据显示,此时箱梁内设备最高温度为45摄氏度,在正常范围内。

包钢股份5台最大吨位的液体罐冶金吊车都在包钢股份稀土钢板材厂。作为吊车点检员,赵延斌和工友们的日常工作就是保证这些“大家伙”的良好状态。以往,完成一天的点检任务,赵延斌他们要多次爬上距离地面27米的吊车箱梁,行走两万多步。如今,只需使用电脑或者手机端就能随时监控设备。一旦参数异常,系统还会自动报警提醒处理。“现在用指尖运动代替了步伐挪动。”说起智能化带来的感受,赵延斌脸上洋溢着幸福。
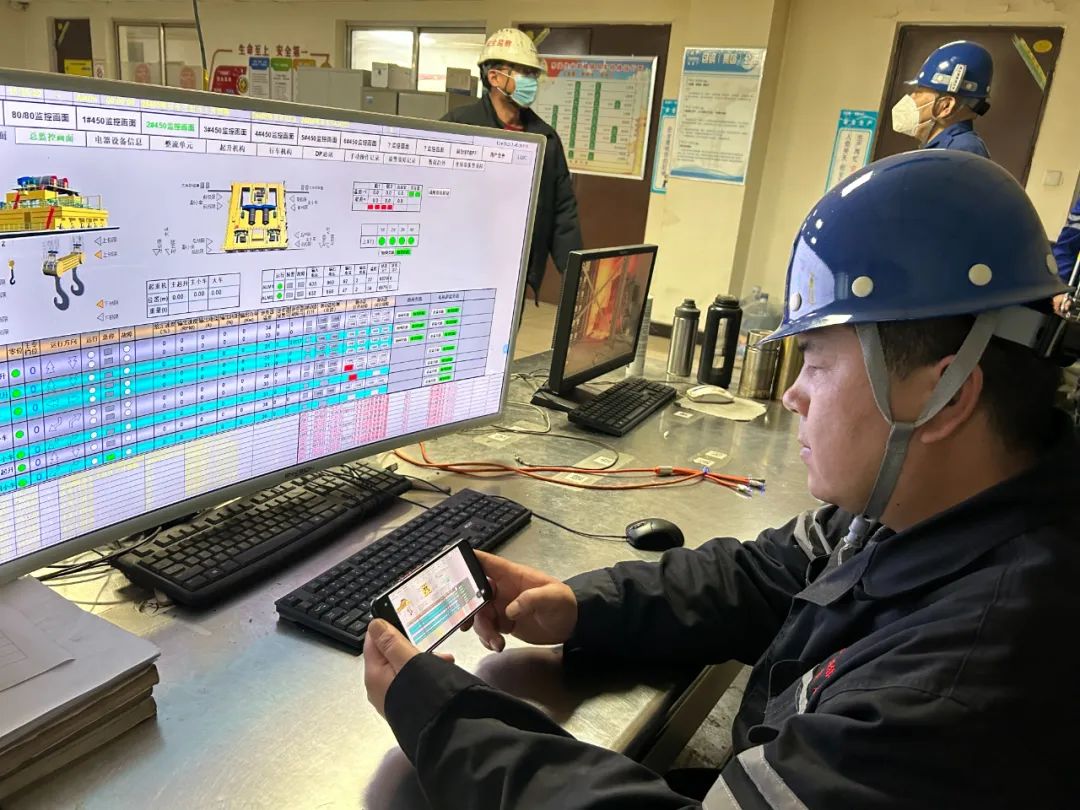
“我们实施这个项目,瞄准的是包钢股份稀土钢板材厂极致效率和极致降本的目标。”吊运作业部党支部副书记王春生道出吊车智能化推进工程的初衷。在包钢股份稀土钢板材厂,吊车是各工艺之间的衔接环节,其故障处理效率直接影响上下游工序的协调。工程以保证职工安全、降低劳动强度、提升点检效率和质量为目的,结合现场需求,以智能化手段推进吊车设备的有效管理,点检机器人是其中最重要的组成部分。此次“上岗”的1号450吨吊车点检机器人由轨道、横行小车、热成像摄像头等组成,通过工业无线网络实时传送信号。这是吊运作业部解放思想、转变思路自主创新取得的研发成果。相较于成套的引进智能点检机器设备而言,这样的大胆尝试不仅加快了智能化脚步,大幅降低了采购成本,同时也具备了设备维护关键技术的自主性。
首台吊车点检机器人“上岗”后,在降低劳动强度、提高工作效率、减少故障率、全面保护设备、改善工作环境、提升本质安全水平等方面作用凸显。下一步,包钢股份稀土钢板材厂将在此基础上继续加快设备维护方式变革的速度,实现吊车设备的点检、定修、安全管理、设备维护的全面智能化。
审核|包钢股份综合部(工会)